Our team of programmers have decades of experience in robotics, PLC and PAC technologies. You can rest easy knowing that your robotics programming and PLCs will be properly integrated. From modifying your current systems to upgrading to 4.0 digital twin.
Using offline tools and programming editors our team will develop, test, and simulate real-world scenarios before installing them onto your system. The wide variety of skills that we have developed in our engineering and programming teams will allow us to incorporate technologies from single-cell robot systems to automation systems with multiple peripherals.
PLC Programming
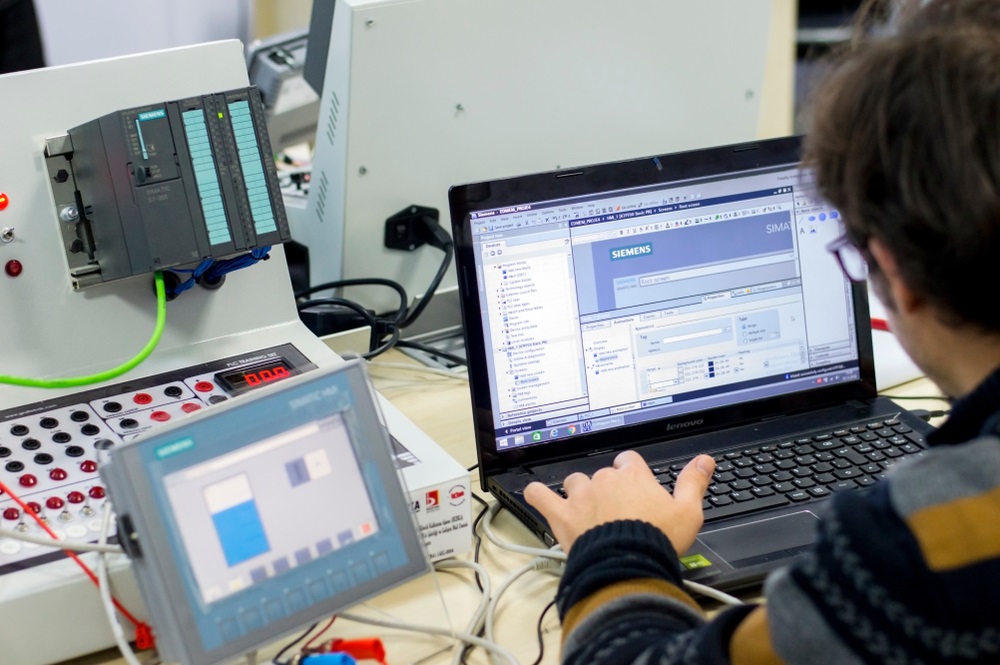
Nearly all automated systems utilize PLCs to control peripheral aspects of the cell. KVM Automation’s team is proficient with all types of PLC. With our knowledge of these systems, we can ensure your system communicates well with the outside world, interfacing with ERP and remote I/O or MES systems. If needed, we can also build your SCADA or MES systems from the ground up.
Our control system engineers are specialized in Industrial Automation and programming of different controllers such as:
- AB ControlLogix, Siemens S7
- Automation Direct logic series
- Design HMI and SCADA with FactoryTalk, AVEVA Edge, or Ignition.
PLC Programming Language
A programmable logic controller (PLC) is an industrial computer that controls industrial machinery.
A few programming languages can be used to create programs for the PLC. These are ladder logic, structured text, and function block diagram. Ladder logic is the most commonly used language with PLCs and has been around since the early 1960s. The name comes from its visual representation of interconnected wires on an electrical schematic diagram resembling a ladder connecting different circuit parts.
Structured Text is less common than Ladder Logic, but it is more readable than Ladder Logic because it uses English-like words instead of numbers or abbreviations (e.g., “IF” instead of “IFLG”). Function Block Diagrams use graphical icons instead of text or numbers for programming instructions.
PLC Programming Devices
PLC programming is the process of creating a program for a PLC controller. The steps involved in this include:
- Selecting the type of PLC programming device to use (such as Progressive Automation’s PanelView Plus)
- Choosing the best software based on your needs (such as Professional Studio)
- Implementing ladder logic determines how inputs and outputs will control functions within the system; This can be done in several ways, but one common method is a standard ladder diagram representing each input and output point on the screen.
It shows how these are connected to create different functions within your machine or system.
Basics of PLC
PLCs are computers. They have their memory, which can store numbers and text.
A PLC can be programmed to do simple or complex tasks, like controlling the temperature of a room or opening and closing the doors of an elevator.
They are used in factories, power plants, oil fields, and chemical plants because they can control machines that need precise amounts of energy or chemicals to process materials.
If something goes wrong with these machines, they could cause injuries to workers or equipment damage that would cost money for repairs.
Most importantly, PLC sensors determine if everything is working properly before sending signals back through wires connected directly to each machine’s mechanical parts.
Hence, they know what needs adjusting without having anyone touch anything manually themselves, which could get them hurt by moving something too heavy without knowing ahead what its limits were designed under normal operating conditions might be like.”
KVM contractors also offer consulting services on said subjects, for more information, click here.
I/O modules
I/O modules are used to connect the PLC to the plant. They can be analog or digital, input or output, and auxiliary. I/O modules are classified by their communication protocol:
- Serial communications (Analog or Digital)
- Modbus RTU (Analog or Digital)
- HART® (Analog Only)
PLC Communication Protocol
- According to Analog, RS232 stands for “Recommended Standard 232” and is a serial data transmission standard that uses voltage levels between -3.0V (low) and +3.0V (high).
Many PLC manufacturers, including Allen-Bradley/Rockwell Automation, Siemens, and Schneider Electric, support this protocol. - RS485 stands for “Recommended Standard 485“, which is used to transmit data over long distances with low power requirements such as only one or two volts per meter (1/2 watt).It has a high-speed response time compared to other protocols, such as Modbus RTU. This is currently one of the most widely used methods for transmitting data among multiple machines within an industrial plant because it can handle up to 32 devices without having any effect on overall system performance due to its ability to handle multiple connections simultaneously without affecting throughput rates significantly lower than other methods like Ethernet which would require additional equipment such as repeater hubs before sending data across long distances; however, this method requires special cables called twisted pair cables because they’re made up entirely out copper wires with different sizes depending on their purpose–for example, if you’re trying communicating with another device located several thousand feet away then your cable should be at least 25 feet long while still maintaining adequate signal strength throughout its entire length so don’t forget about this important fact when making purchases later down-line!
HMI and SCADA Communication Protocol
- HMI and SCADA communication protocol is used to communicate between PLC and HMI/SCADA. It uses simple ASCII characters but also includes binary and hexadecimal values. The protocol is generally divided into three parts: the initial handshake, the data exchange part, and the final handshake.
KVM Automation Offers the Right Integrated PLC Programming Solutions for Your Industry
Automation is the future. Over time, it will replace your repetitive tasks with automated processes.
By letting KVM Automation to take care of programming your PLCs you could easily save money and be more productive in your work life by automating processes that would otherwise take up a lot of time on an employee’s schedule. Contact us today by filling out the form below and we’ll get in touch with you shortly!